
Our visit took place before the Covid-19 pandemic and, like so many of our creative industries, this family-run business has faced unprecedented challenges in the months that have followed. We have long admired Beckford Silk's creativity, passion and expertise and, as we celebrate their work below, we also wish them the very best as they adapt and rise to the challenges of the current situation.
Beckford Silk was founded in 1975 by James and Marthe Gardner, at their home in the village of Beckford, near Tewkesbury. Originally in the catering industry, James had a real passion for colour and began experimenting with printing silk in a workshop at the bottom of the garden. Years of research and development resulted in James receiving his first big order in 1978, which firmly established Beckford Silk as the main supplier of printed silk for the heritage market in the UK. As demand increased in the late 1980s and early 1990s, they moved into custom-built premises in the village and this is where you’ll find Beckford Silk today.
A Family Affair
A 50-minute drive from Stratford-upon-Avon and we arrive at an impressive building nestled in the Gloucestershire countryside. We are met by Anne Hopkins, Director of Sales and Design and the daughter of James and Marthe. It’s still very much a family business as we are introduced to Robbie, Production Director and Anne’s brother. They explain that their dad James still comes in at 7am to dye silk and their mum usually works in their shop on site. It’s very clear talking to both of them that they share their dad’s passion for all things silk and are working hard to future proof the company by using new technologies, while maintaining Beckford’s established arts and crafts roots.
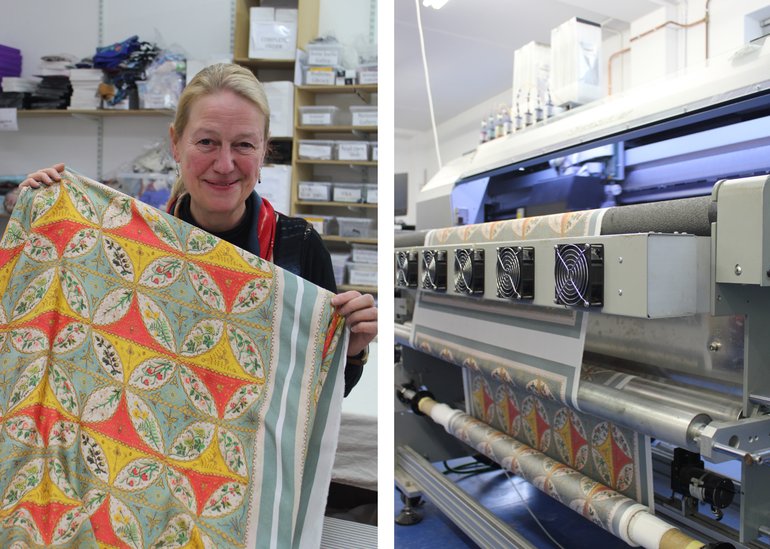
Beckford have the largest selection of dyed silk in
the UK, from silk crepe de chine to silk georgette, and they are all dyed by
hand on the premises. We start with a tour of the dye room and are shown the
books of colour swatches with hand-scribbled recipe quantities that date back
to the 1970s. These books are a thing of beauty in themselves.
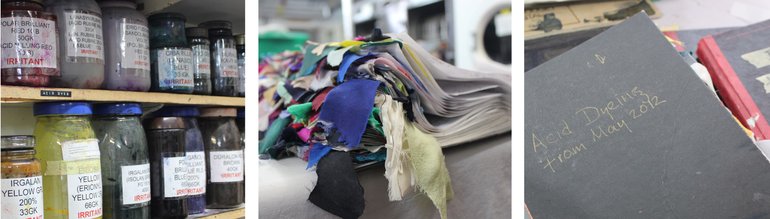
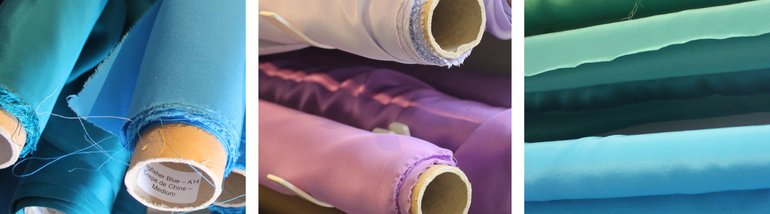
From there we move to the design studio. As is the
case with our own scarf designs, each design concept usually takes inspiration
from an object or image in a museum or gallery collection. Elements from the
design are painstakingly hand drawn and scanned into a computer, where they are
digitally manipulated. Anne explains that the hand drawn element is vital to
what they do: if you make a mark on a piece of paper you have expression, lines
vary in thickness and these handmade irregularities are retained right through
to the finished silk product. Once the design is approved, they can begin
proofing the design on silk to get the best possible print and colour. This is
achieved by either screen or digital printing.
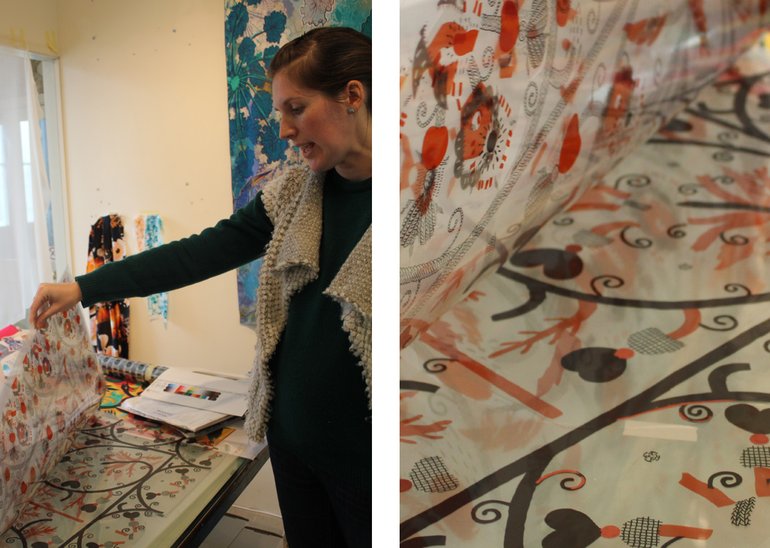
Digitally Printed Silk
We are taken through to the digital print room where three impressive paper printers converted to textile printers are whirring away, printing our latest silk scarf. Beckford is the only company in the UK that digitally prints acid dyes on silk and they’ve just increased their capability with a new Japanese printing machine. It's the only one in the world and so new that the software isn’t ready yet. Beckford still screen print some silk, but the quality of digital printers, and the fact that they can print 10 metres of silk an hour, makes digital a more efficient process. Anne comments that with the amount of proofing and fine tuning that goes into digital printing it’s as much a human skill as screen printing.
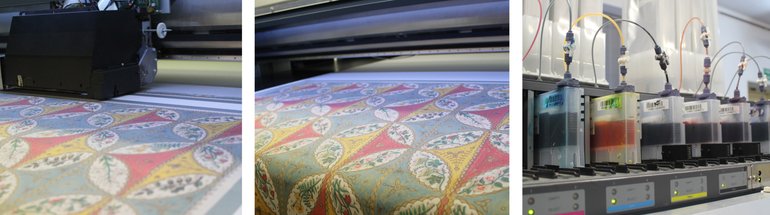
How does the process work? The silk is coated with gum and chemicals (similar to screen printing) before it’s attached to a sticky belt on the printer. It is crucial that it goes through the printer straight to avoid printing off the grain. The printers use a combination of eight different acid inks and once a design is printed, it is dried, steamed and washed to fix the colours. When it's dry, the silk is still full of gum, so it’s added onto the hooks of a star frame, starting from the centre and spiralling outwards, with sheets of calico in between to prevent any touching. The frame is then lowered into a pressure steamer by an excellent low-tech contraption (created by dad, James) of two fishing rods and a pulley system. The steam fixes the colour and releases the gum which is then washed away.
For the end drying process, we are then taken to see the very clever ‘clip stenter’ machine, which is over 100 years old. It has two large rotating chains and the silk is fed through an infrared oven to thoroughly dry and remove all the creases. The silk is then thoroughly checked by eye to make sure the print is perfect.
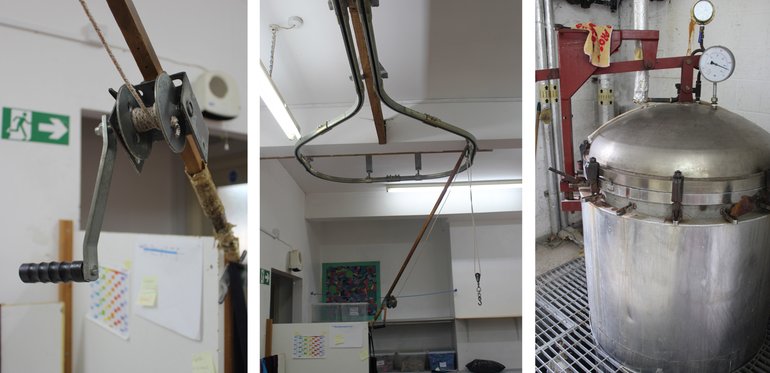
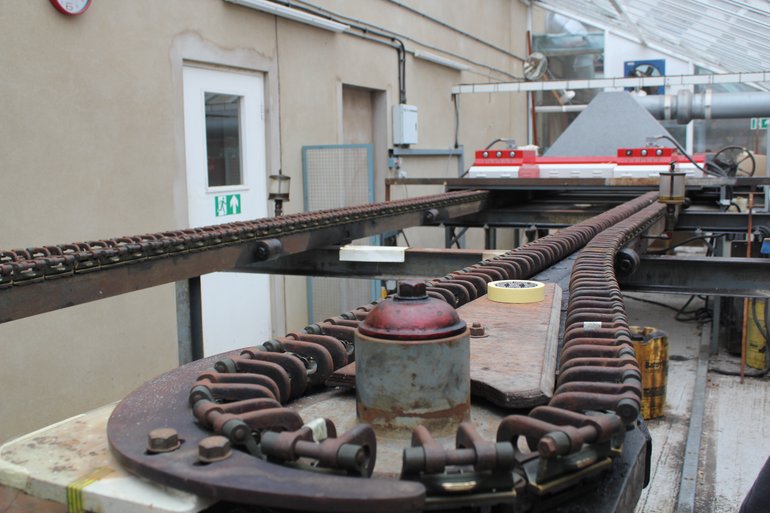
The finishing of the edges is the final part of the process and the majority of Beckford Silk scarfs are hand rolled. They have the largest team of ‘hand rollers’ in the country. It’s a very skilful job and it takes some time to perfect the technique. Once trained, a hand roller can complete three 90cm scarves in an hour. You can watch how hand rolling silk is done here. Finally the scarves are ironed, folded and packaged by hand. We meet Naomi, who effortlessly demonstrates the technique with a very hot iron!
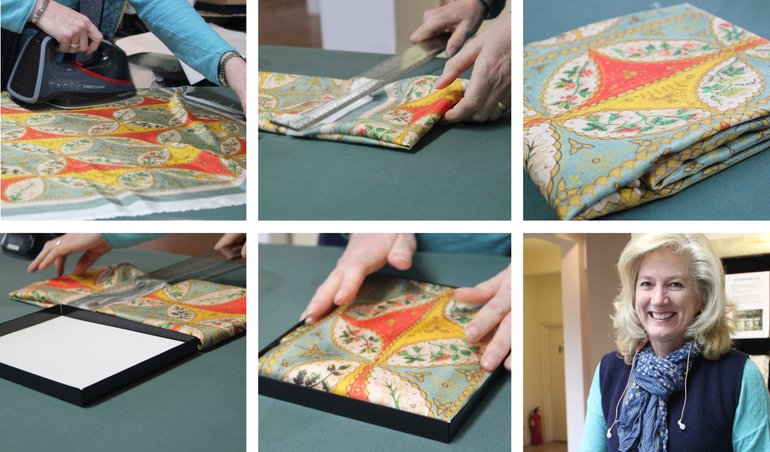
We leave with a renewed appreciation of the attention to detail undertaken in the production of our scarves, and admiration for the Beckford team's ability to embrace the very latest printing techniques while still holding on to the artisan skills of hand rolling and dyeing.
See our range of exclusive handmade Beckford scarves.
You can also learn more about silk printing and plan a visit to Beckford Silk.
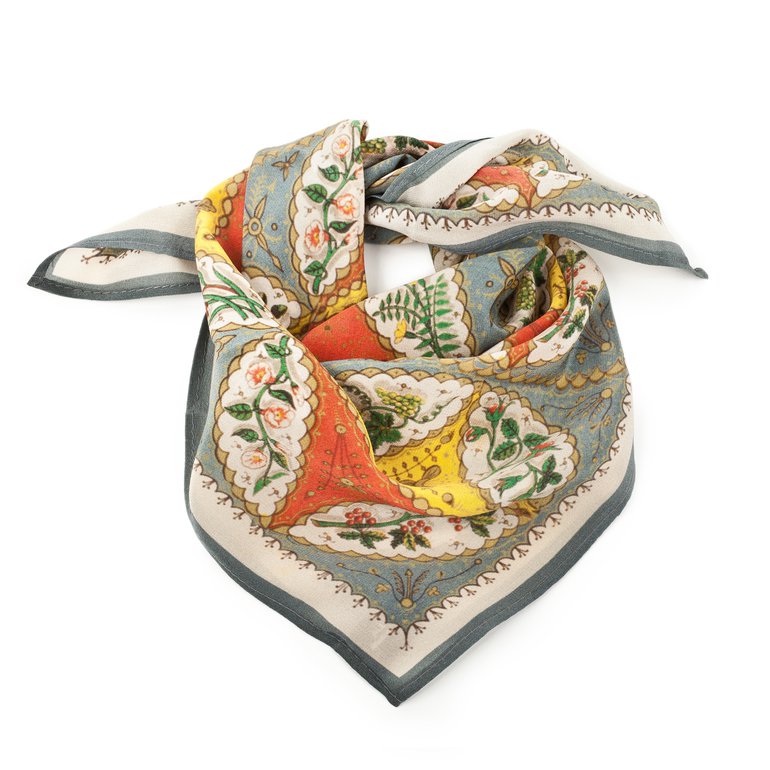